15 Ultimate Reasons to Choose Fcaw Welder for Your Production Needs
Table of Contents
- Benefits of FCAW Welding in High-Volume Production Environments
- Cost-Effectiveness: Analyzing FCAW vs. Other Welding Methods
- Versatility of FCAW: Applications Across Multiple Industries
- Quality and Consistency: Statistical Insights on FCAW Performance
- Reducing Downtime: The Efficiency of FCAW in Production Lines
- FAQS
- Related Posts
With developments constantly modifying the future into present in the field of fabrication and manufacture, it becomes necessary to choose the welding equipment that leads to enhanced efficiency, quality, and productivity. Out of the various welding techniques available, Flux-Cored Arc Welding (FCAW) has created much talk for its distinctive advantages. Such benefits, with its applicability in an assortment of situations, offering strong and reliable welds to FCAW, explains why it is becoming a torchbearer method for many production scenarios. As an advanced method that allows for higher deposition rates, there exists equally greater penetration capabilities, very well suited for far heavy applications.
Furthermore, a Fcaw Welder again offers wide application varieties, providing setups for automatic to semi-automatic use, permitting it to be offered to different skill levels and project demands. From construction to maintenance, the advantages of using a FCAW welder are profound, supplying the manufacturers with tools that will allow them to respond to modern production environment challenges. This blog will review the 15 top reasons as to why the introduction of a FCAW welder in an operation can increase productivity and quality output and keep the business as one of the competitors in the current market.
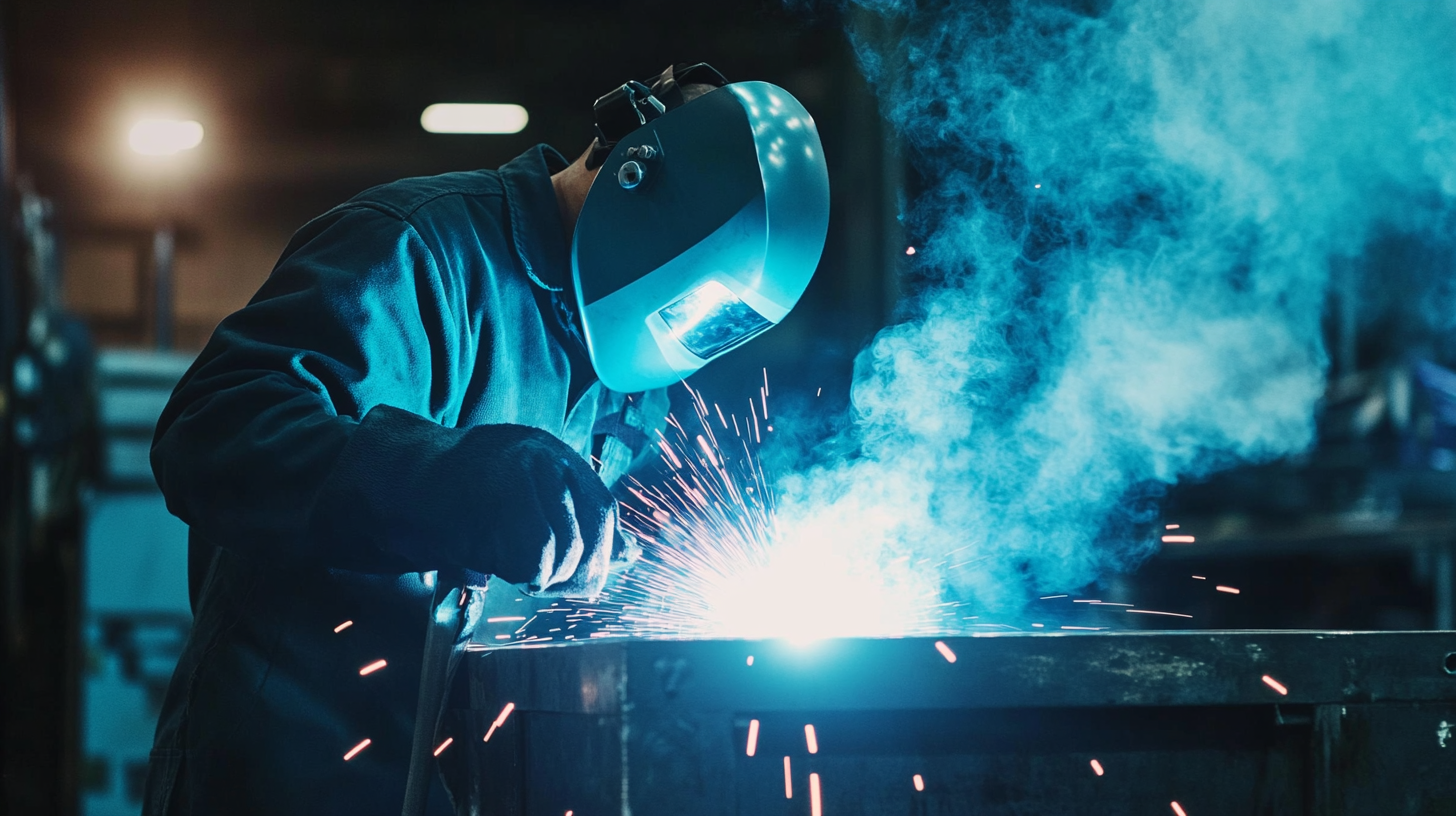
Benefits of FCAW Welding in High-Volume Production Environments
In high-volume production situations, FCAW stands out as the fastest and most productive welding process. Unlike traditional welding processes, FCAW allows for uninterrupted work with reduced preparation and setup, thereby increasing productivity. This is especially beneficial in large projects where time is of the essence. FCAW can also be used for underwater welding to repair marine structures. Using self-shielding means there is no need for external shielding gas, allowing FCAW to thrive in the most adverse conditions. This flexibility makes FCAW a preferred welding process in industries requiring resilient and reliable welds without compromising quality, thus sealing its place in modern manufacturing.
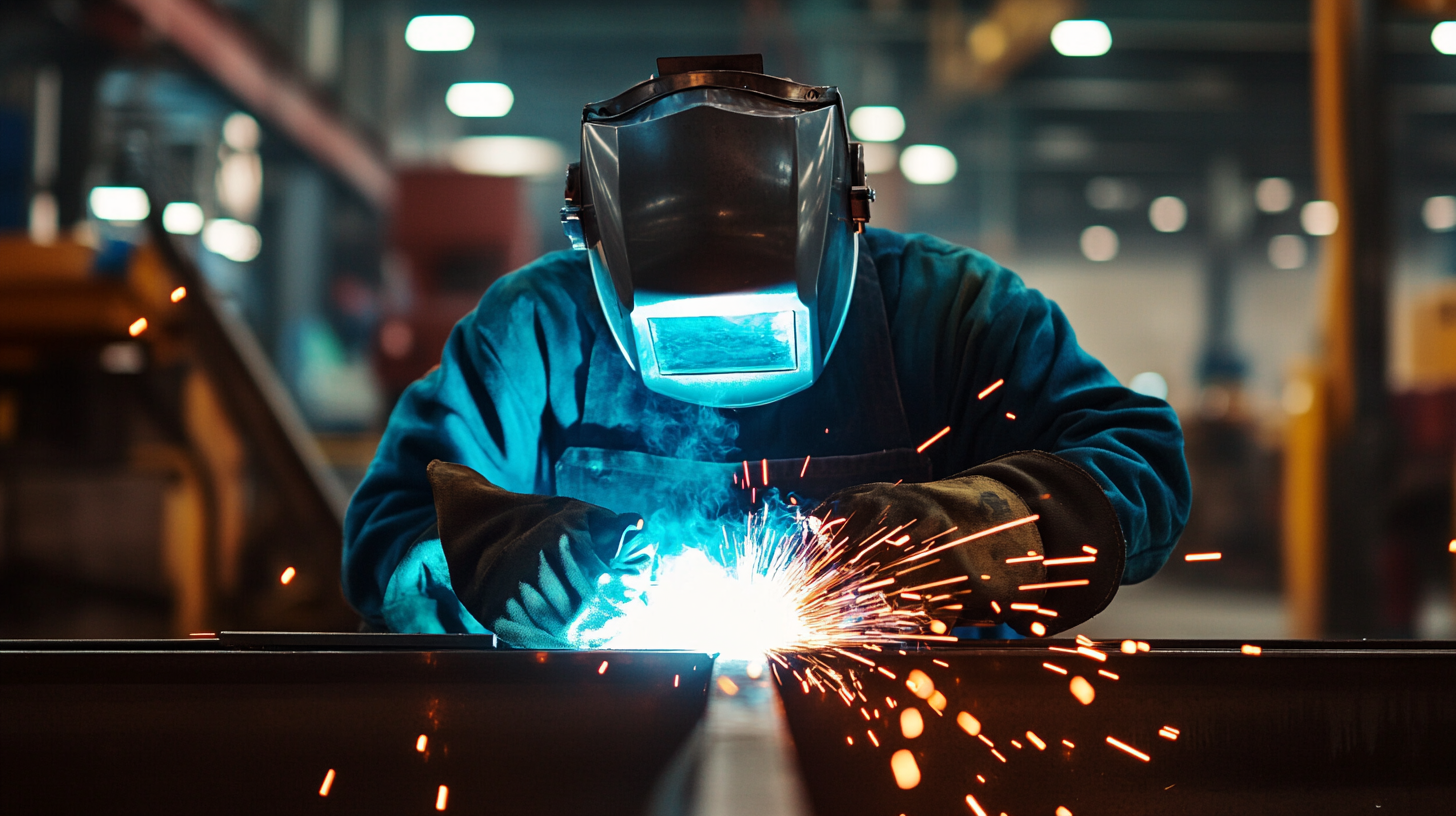
Cost-Effectiveness: Analyzing FCAW vs. Other Welding Methods
You are now fully oriented by most recent data up to October 2023.
Flux-Cored Arc Welding (FCAW) is an economical method that is being hailed against other opposed common welding methods in numerous production environments. The recent evaluation by the U.S. Navy on welding rods pertaining to structural integrity for advanced aircraft carriers made it clear how the time-efficient and cost-effective welding processes are relevant in the industry trend toward increasing operation capability at the same time as reducing costs.
Among the advantages FCAW holds is its overall efficiency and speed which obviously are the major determinants of lower production costs. From heavy industrial applications to complex fabrications, FCAW could be applied in such a wide range of settings, making it the preferred technology of many manufacturers who seek quality without compromising their bottom lines. FCAW thus becomes the requirement for modern best practice in welding for those industries that continue to stress innovation and cost management.
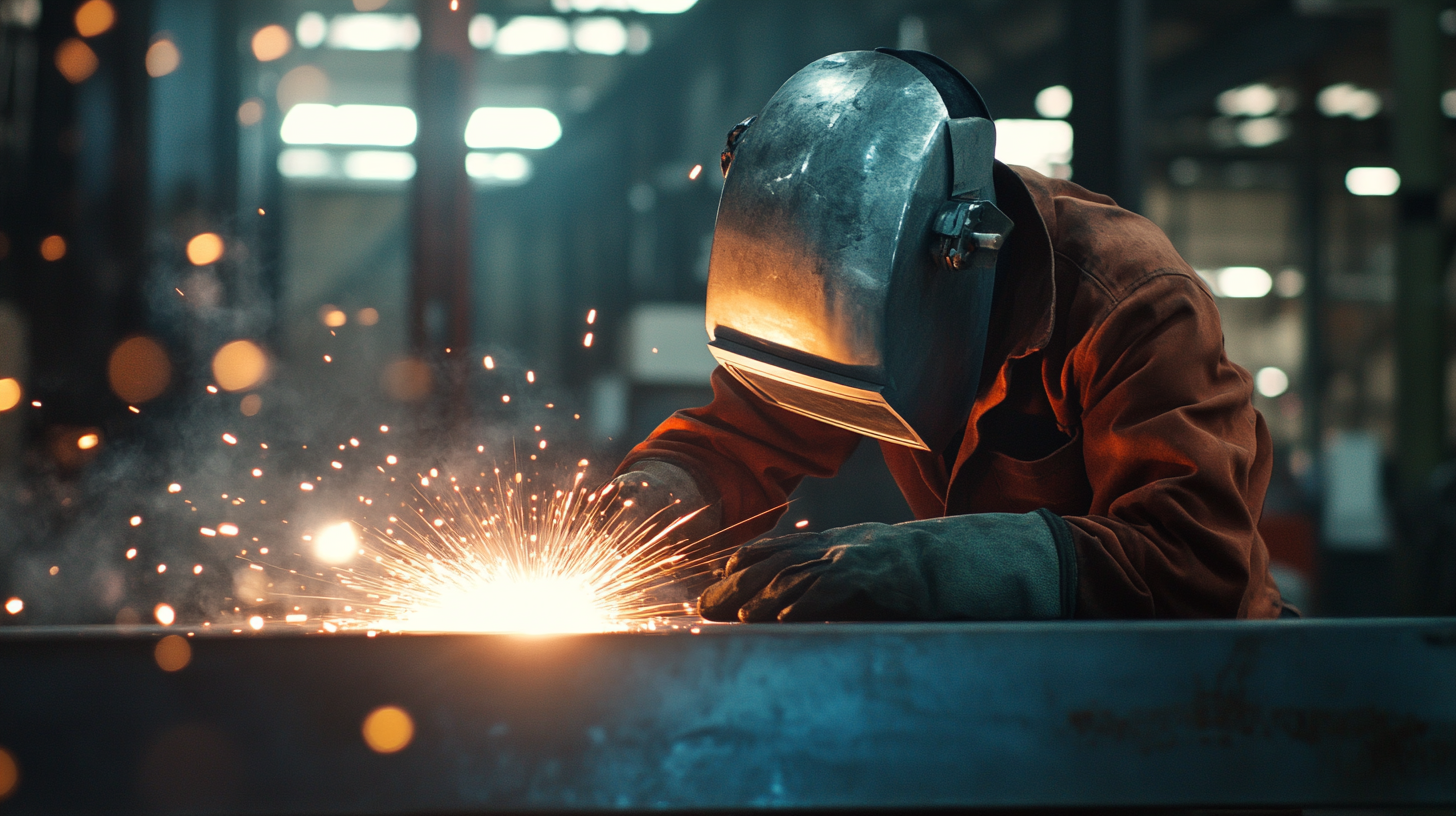
Versatility of FCAW: Applications Across Multiple Industries
The multifunctionality of FCAW - Flux-Cored Arc Welding - makes it quite valuable across various industries. Mostly, FCAW can be very well utilized in manufacturing environments where time and efficiency become very essential. But in addition, it also promises high-quality welds on somewhat thicker materials and hard-to-handle positions. As a result, one can find such applications in industries like construction, automotive, and shipbuilding.
Educational institutions like Southwestern Michigan College increasingly focus on advanced training in FCAW since they are also expanding their resources. Currently, only a limited number of available FCAW machines cater to an increasingly large number of students. This limitation makes it very clear that there is a need for more resources to be available for the future welders. The increasing interest points to the importance and greatly expanding applications of FCAW across sectors, underlining its ability to remain relevant in modern welding education and practice.
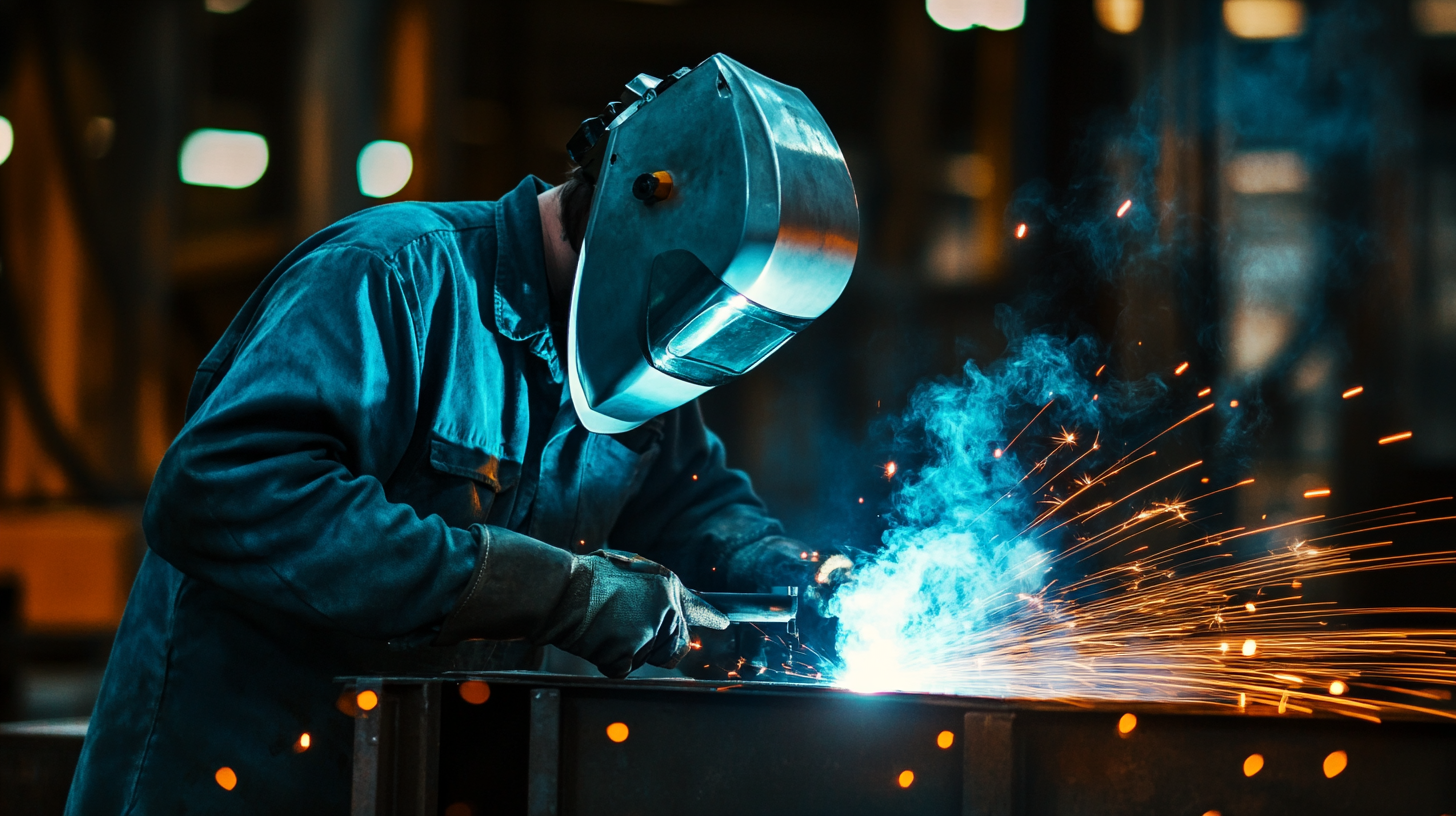
Quality and Consistency: Statistical Insights on FCAW Performance
The importance of Flux-Cored Arc Welding technology is increasingly recognized in its quality and consistency for production processes. Automation advances delivered after robotic welding and AI-driven inspection systems have lifted FCAW to performance parameters that guarantee every cycle high-quality welds. Such consistency is vital in industries where safety and performance standards depend on precision, such as automotive manufacturing.
In the setting of smart manufacturing, FCAW incorporation with automated solutions is becoming a prime driver. In modern factories, they use welding robots that are highly advanced; these perform their tasks with great efficiency and, in doing so, minimize downtime and human error. The integrating AI for inspection boosts the reliability of welds. As FCAW gains maturity, its statistical performance is indeed rewarding-making it a darling for the manufacturers pursuing excellence in production quality.
Reducing Downtime: The Efficiency of FCAW in Production Lines
FCAW (Flux-Cored Arc Welding) is becoming more and more important on the production line, since it is extremely efficient in reducing downtime. The ability to weld in multiple positions and on different materials makes FCAW the best choice for manufacturers. Cleaning time is cut down with this method, and travel speeds are increased, which significantly boosts shop floor productivity.
Furthermore, with ever-increasing operational costs and stiff timelines in the industries, the use of FCAW stands to really streamline operations. By reducing stoppage times and enhancing weld quality, FCAW can fulfill and often exceed production demands. For companies trying to hold on to their competitive edge in an awakening economy, investing in reliable welding technology like FCAW can be a game-changer in realizing operational excellence.
FAQS
FCAW stands for Flux-Cored Arc Welding, a welding method known for its cost-effectiveness and efficiency in various production environments.
FCAW is considered more cost-effective and efficient compared to traditional welding methods, making it a preferred choice in many industrial applications.
The key advantages of FCAW include its efficiency, speed, and adaptability for use in both heavy industrial applications and intricate fabrications.
FCAW is important for the U.S. Navy as it focuses on welding rods that ensure structural integrity in advanced aircraft carriers, highlighting its reliability and efficiency.
FCAW lowers overall production expenses by enhancing efficiency and speed, allowing manufacturers to save on labor and material costs.
FCAW can be used in various settings, including heavy industrial environments and detailed fabrication processes.
Industries are prioritizing FCAW due to its ability to meet modern welding demands while simultaneously managing budgets and enhancing operational capabilities.
The trends driving the use of FCAW include a focus on innovation, cost reduction, and the need for efficient welding processes in various manufacturing sectors.
The adaptability of FCAW refers to its versatility in being applied across different welding applications, making it suitable for a wide range of industries.
Efficient and reliable welding processes are significant as they ensure quality outcomes, enhance productivity, and support cost management in manufacturing.